Home”Boost Your CAD CENTRE Skills with Expert MASTERCAM Tutoring and Training” https://fortressinstitutetraining.com/
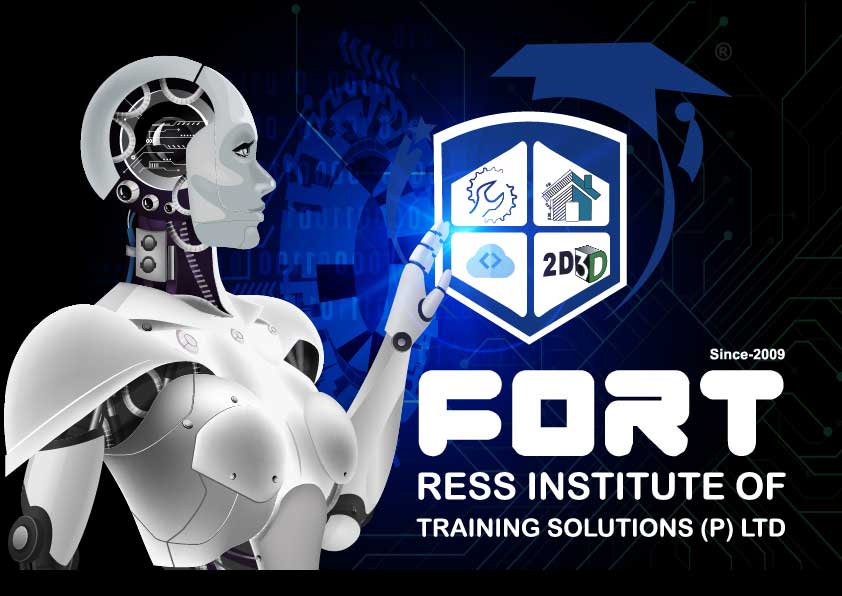
CAD Course
in Coimbatore
No.1 CAD Training Institute in Coimbatore with 100% Placement Record.http://fortressinstitutetraining.com
Get 40% Off – Call 95666 08904 Now!
CAD Course in Coimbator with placement
AutoCAD Mechanical is a specialized version of AutoCAD tailored for mechanical engineering design and drafting. Below is an outline of key subjects and areas of study within AutoCAD Mechanical:
Placement of FORT RESS INSTITUTE OF TRAINING SOLUTIONS PVT LTD
UPCOMING CLASSES BELOW Get 30% Off
Choose the right way to upgrade your career.
CAD/CAM SOFTWARE TUTORING
MASTERCAM SOLUTIONS FOR MANUFACTURING
2D | 3D ANIMATION VFX TUTORING
MECHANICAL PRODUCT DESIGN
SOFTWARE DEVELOPMENT COURSES
CERTIFICATE IN ARCHITECTURAL DESIGN
3D ANIMATION INTRO TO STORYTELLING CHARACTER DESIGN
CERTIFICATE PROGRAMS PYTHON FOR BEGINNERS
WhatWe’reOfferingWhatWe’reOfferingWhatWe’reOffering
Keep your company current with the latest technology Service
Learn The Latest Software From Certified Experts FORT RESS Offers Customized CAD Or BIM Training By Autodesk Certified Professionals. Training Is Available On-Site Or Off-Site, With One Computer Per Student During Class Time.
Get Certified
IIE
Official Autodesk certificates of completion are provided to all students completing our courses in AutoCAD or Revit. CAD Simplified also issues certificates of completion in all other software courses
One Pc Per Student
Software installation assistance
Classrooms are equipped with one PC computer per student, kept up to date with the latest software. All CAD classes support MAC and PC users. Students are welcome to bring their own MAC laptop to practice during the class time. We point out the differences between the two versions.
Hands On Training
Take Home Reference Sheets
At CAD Simplified We Focus On Individual Attention And Clear Communication After Explaining Each Concept, Instructors Insure That All Students Are Caught Up And Able To Apply The Tools They Just Learned.
Small Class Size
& 8 Students Max
Classes Comprise A Minimum Of 3 Students And A Maximum Of 8. This Ensures You Get The Personal Attention You Deserve In An Environment Conducive To Sharing Knowledge And Learning From Your Peers.
Real Life Examples
& Analysis
Course Work Is Based On Industry Standards And Uses Real-Life Examples That You Are Most Likely To Encounter In Your Professional Career.
Revolutionizing Precision and Efficiency: Meet the New Mastercam Deburr
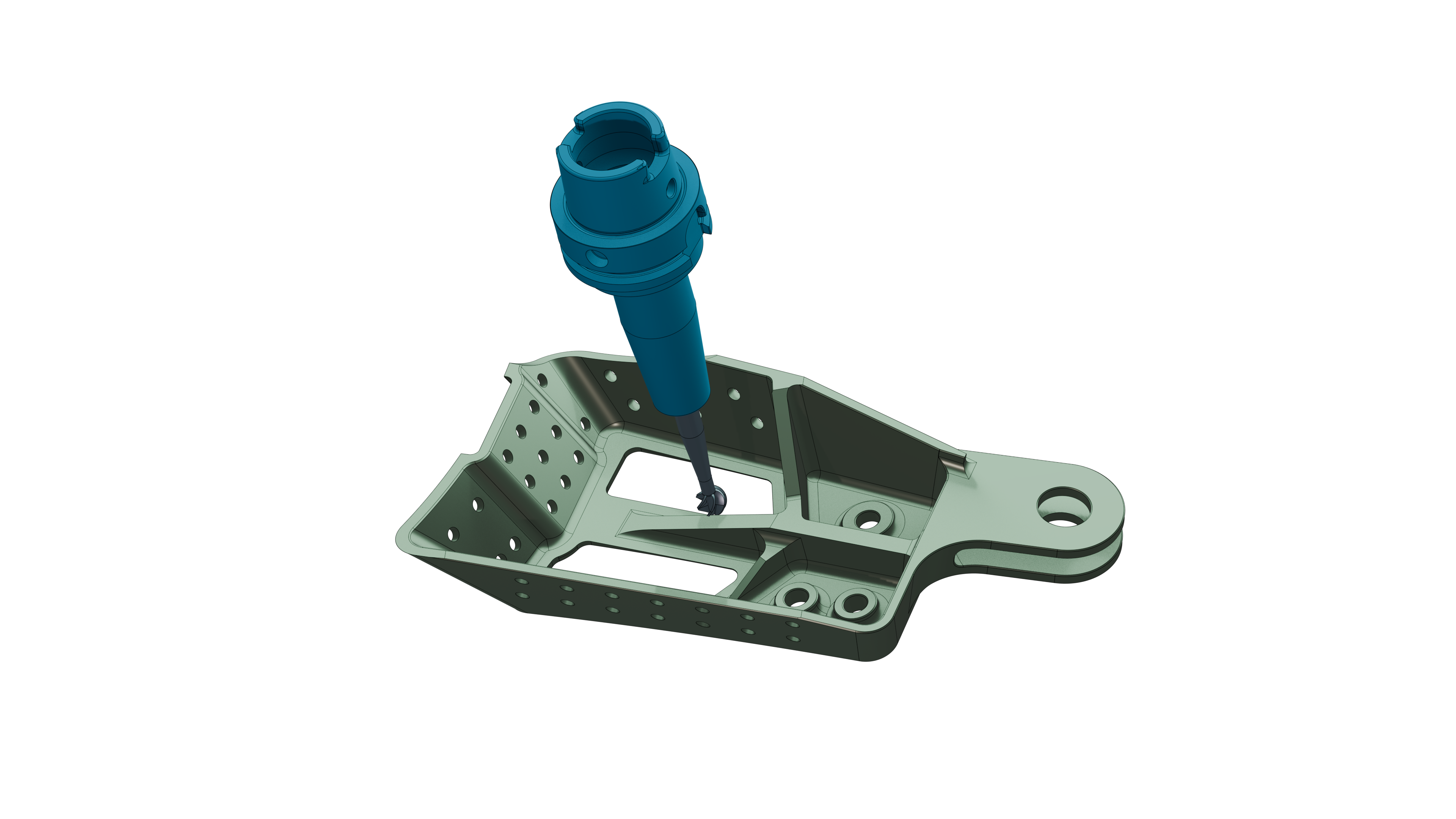
Mastercam 2025: Enhancing Dynamic Toolpaths with Finish Passes
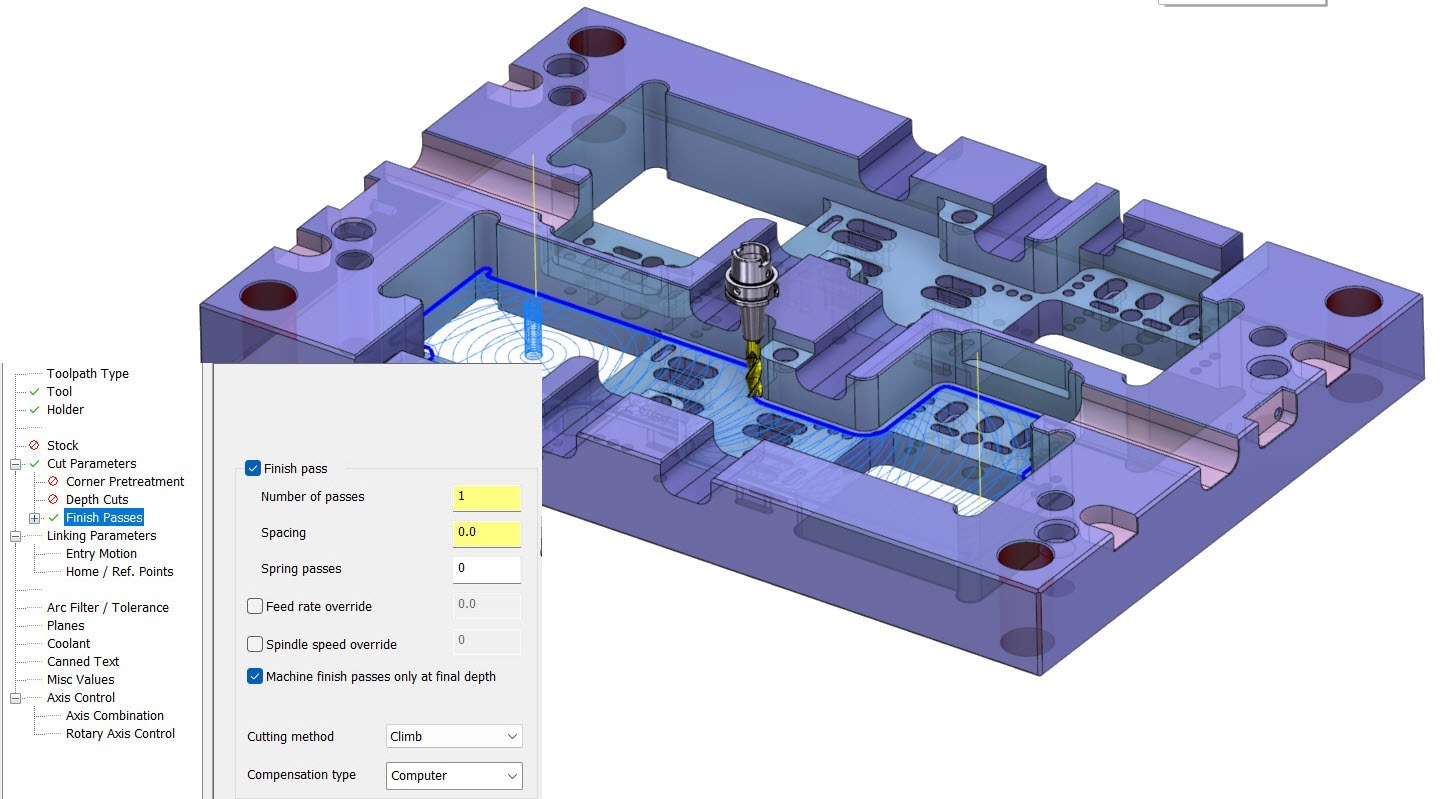
In the fast-paced world of manufacturing, efficiency is key. Mastercam’s Dynamic toolpath functionality has long been a beacon of innovation, helping machinists reduce cycle times, extend tool life, and lessen wear and tear on their machines.
With the release of Mastercam 2025, this game-changing toolpath motion has received a significant upgrade with the introduction of finish passes. This new feature promises to take your machining operations to the next level. Let’s delve into how this works and the benefits it brings.
The Evolution of Dynamic Toolpaths
Dynamic toolpaths in Mastercam revolutionized machining by employing a continuous, optimized cutting motion. Unlike traditional toolpaths that follow a more segmented approach, Dynamic toolpaths keep the tool engaged with the material more consistently. This approach removes material efficiently but can sometimes leave behind tool marks as the tool re-engages and exits the cut repeatedly.
In scenarios like machining outside walls or complex geometries, these tool marks can be more pronounced. This is where Mastercam 2025’s enhancement comes into play. The new finish passes feature is designed to address these imperfections, offering a more refined and polished end product.
Understanding Finish Passes
With the integration of finish passes into Mastercam 2025, users can now clean up these residual marks with ease. Let’s take a closer look at how this feature works:
Configuring Finish Passes: When setting up your toolpath, you can now activate finish passes and specify the amount of material to leave for finishing. For instance, setting a 0.5 mm offset for a single finish pass will ensure that the toolpath is adjusted to remove the remaining material with precision.
Finish Pass Settings: Mastercam 2025 offers a variety of finish pass settings to fine-tune your operation. These include options for spring passes, which help in achieving a smoother surface, feedrate overrides, and adjustments for cutting methods and compensation types. These settings allow you to customize the finishing process to meet the specific requirements of your job.
Lead-In and Lead-Out Options: The software also includes an extensive range of lead-in and lead-out settings. These controls dictate how the tool enters and exits the finishing pass, ensuring smooth transitions and reducing the risk of surface imperfections.
Toolpath Recalculation and Safety
Once you enable finish passes and regenerate your toolpath, you’ll notice the addition of extra toolpath motions designed to clean up the walls and remove the residual material. This recalculated toolpath helps in achieving a more refined surface finish, addressing any leftover tool marks.
However, dynamic toolpath motion can sometimes present challenges, especially if the tool does not fully engage with the material due to the radius or shape of the geometry. In such cases, the “Minimize Burial” option ensures that the tool remains in a safe operational environment, mitigating potential risks associated with toolpath engagement.
Benefits and Applications
The addition of finish passes to both 2D Dynamic Mill and Area Mill toolpaths in Mastercam 2025 is more than just a feature upgrade—it’s a significant boost to machining efficiency. By incorporating this functionality, users can save valuable programming time and expedite the transition from toolpath creation to machine operation. The ability to refine toolpaths directly within the software reduces the need for additional post-processing or manual finishing, streamlining the manufacturing process.
Ready to get started?
Mastercam 2025’s enhancement of Dynamic toolpaths with the introduction of finish passes offers a powerful solution for achieving superior surface finishes and optimizing machining operations. Whether you’re working on intricate components or high-volume production, this new feature is designed to enhance your workflow, improve product quality, and ultimately, drive greater efficiency in your manufacturing processes.
Contact your Mastercam Channel Partner today to get started!
7 New CAD Features to Explore in Mastercam 2025
Mastercam Design is a computer-aided design solution that simplifies the creation of even the most complex parts with a robust suite of CAD tools. Mastercam 2025 is here and elevates your machining experience with powerful toolpaths, flexible tool motion, and our most intuitive interface yet. Here are some top CAD features—and how they can help your shop.
1. Analyze Deviation
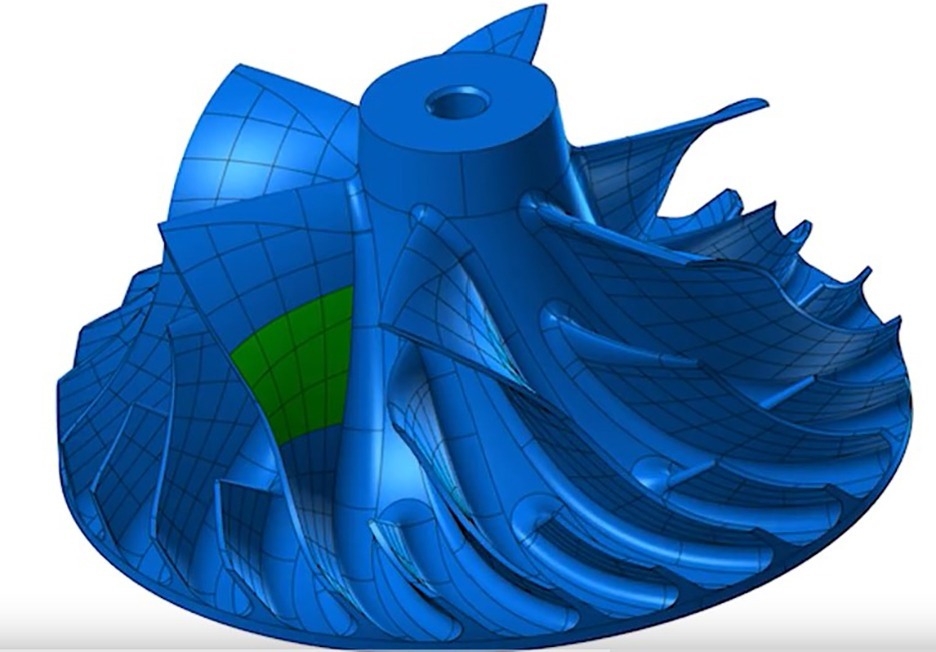
The engines that individual CAD systems use to generate geometry can produce models that vary from system to system. If you have to import information from other packages, you may need to identify deviation between imported entities and their Mastercam counterparts. Mastercam 2025 now includes deviation analysis that allows you to compare any combination of points, curves, surfaces, bodies, and faces.
The new Analyze Deviation function analyzes the differences between different kinds of entities and applies a color-coded “heat map” to the geometry to display deviations within the graphics window.
2. Modified Mesh Geometry
Mastercam 2025 no longer removes associated edited mesh geometry from a toolpath operation. Now, if you edit your associated mesh, there is no need to reselect your geometry; you only need to regenerate the toolpath, saving both time and money.
3. Nesting Results
Three new interface options are now available to improve the visibility of your nested parts in the Nesting Results dialog box. Select the White background and Black part geometry options to instantly view high contrast previews of your nested parts. You can also further adjust part definition by selecting a line width from the Line width drop-down menu.
4. Multiple Nesting Reports
Sometimes it’s important to compare nesting strategies to see which would work best for your setup. In previous versions of Mastercam, this required the extra step of renaming the XML in the ActiveReports Selection dialog box, or copying and renaming the file after you generated it. Now, Mastercam generates a unique, randomly named XML file each time you run a Nesting report, eliminating this extra step.
5. Control Processing Time for Solid Fillets
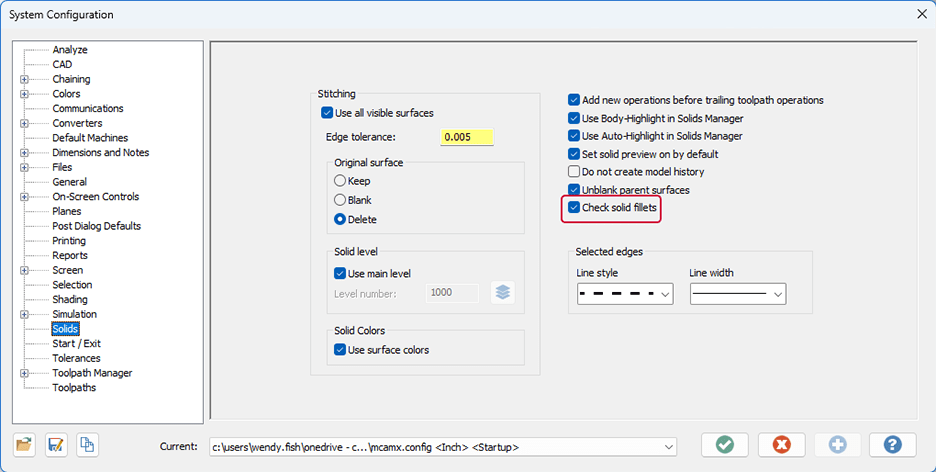
Modifying complex solids can be time-consuming due to the amount of validation Mastercam has to do to read the file and process the changes. To save your shop’s time, we have added the ability to control how Mastercam reads the filleted edges of your solids. Choose to either control this behavior globally for all your solids or locally for individual solid bodies.
Deselect the new Check solid fillets option to stop Mastercam from validating the blended edges of all solids, which can significantly reduce processing time.
The new Check Results controls allow you to override your system configuration settings whenever you feel it is necessary.
6. Duplicated Solids
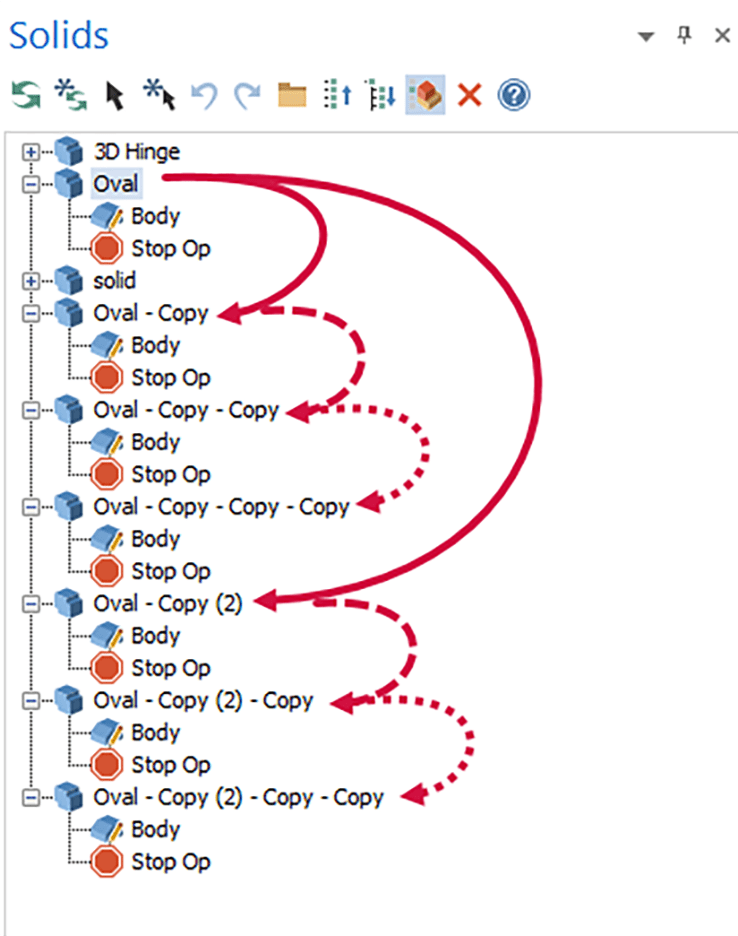
In previous versions of Mastercam, if you needed to create multiple copies of a solid in the Solids Manager, it could be difficult to keep track of your results. To help you, Mastercam 2025 automatically renames duplicated solids according to Windows standards. Now when you duplicate a solid, Mastercam appends “-Copy” plus a number to indicate if there is more than one duplication.
When you copy a solid that has already been duplicated, Mastercam continues to add “-Copy” to the name of the solid.
Mastercam adds both types of duplicated solids to the bottom of the Solids History Tree. If you create multiple duplications of a solid model consistently, it is recommended that you give your solids unique names to minimize any confusion.
7. Define a Sweep Angle
Mastercam 2025 reduces the time you spend creating CAD for CAM by now allowing you to define a specific sweep angle when you use the Arc one entity and Arc one point methods in the Arc Tangent function. In previous versions, you would have had to adjust the arc in a separate step because the arc angle was predefined at 180 degrees.
Want More Information?
If seeing the top CAD features has you ready to update or you want to learn more about what Mastercam can do for your shop, please reach out to your local Mastercam Channel Partner. Or, if you’re ready to explore CAD features on your own, download the free Mastercam Learning Edition.
Explore the Latest Milling Enhancements in Mastercam 2025
Mastercam Mill is fully associative CAD/CAM for 2 1/2- to 5-axis machining and delivers streamlined mill programming and toolpaths powered by Dynamic Motion® technology. Mastercam 2025 is here to elevate your machining experience with powerful toolpaths, flexible tool motion, and our most intuitive interface yet. Here are some top Milling features—and how they can help your shop.
1. Mastercam Deburr
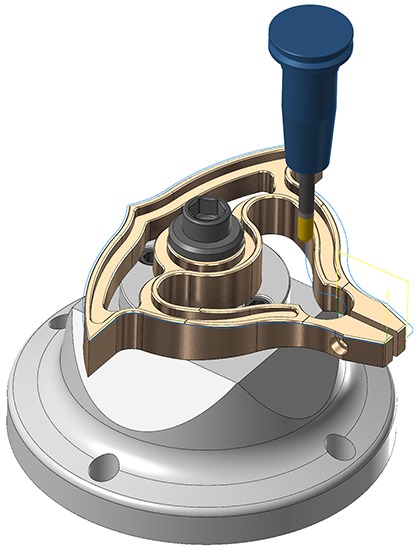
We are excited to announce the release of Mastercam Deburr, the ultimate solution for efficient and precise deburring. The Mastercam Deburr Add-On offers significant advancement for users of Mastercam 2D and 3D Milling, Mastercam Router, and Mastercam Mill-Turn.
This advanced solution features automated edge finishing which streamlines the deburring process, enabling precise control and minimizing the need for manual finishing.
Mastercam Deburr tackles complex edges on non-prismatic shapes with ease, and automates complex deburring tasks, saving valuable time and greatly enhancing the quality of the final product.
Mastercam Deburr simplifies deburring with automatic edge detection and intuitive controls, ensuring a faster and more accurate deburring process.
2. Finish Passes
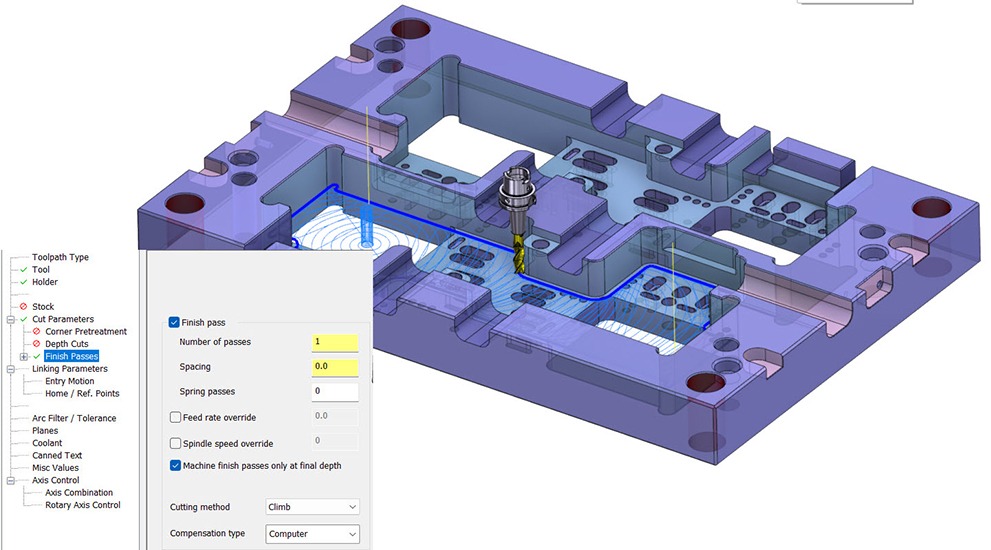
Mastercam 2025 introduces the ability to add Finish Passes to 2D Dynamic Mill and Area Mill toolpaths.
Use the new Finish Passes page to add high speed finishing passes along the selected boundaries of the toolpath. After selecting the Finish pass option, use the other parameters to further define the finish pass, such as feed rate and spindle speed overrides.
Use Spacing options to ensure there is material for the finish passes and use the new Lead In/Out page to set specific lead in and out options for finish passes.
3. Solid Hole Selection
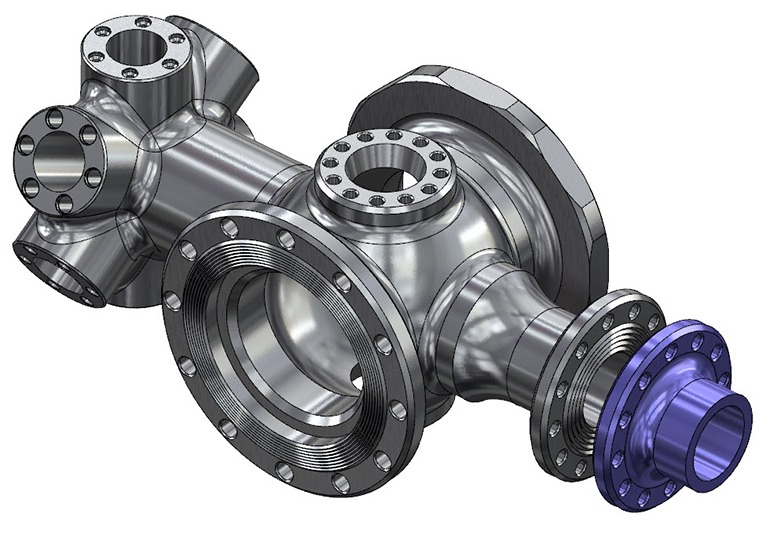
Mastercam 2025 introduces significant enhancements to the Solid Hole Selection feature, which is integral for those utilizing Hole Making and Process Hole toolpaths. The changes associated with this update create a more efficient, precise, and controllable hole selection.
The Solid Hole Selection update encompasses many new behaviors for selecting holes such as simplified selection rules, multiple hole types are allowed in a single toolpath, and segment selections from the same hole are always joined together into a single feature. Other features include solids history selection and selection across multiple solid bodies, as well as a unified selection experience when working with native Mastercam solid hole features or imported neutral CAD formats.
4. Thread Milling Features
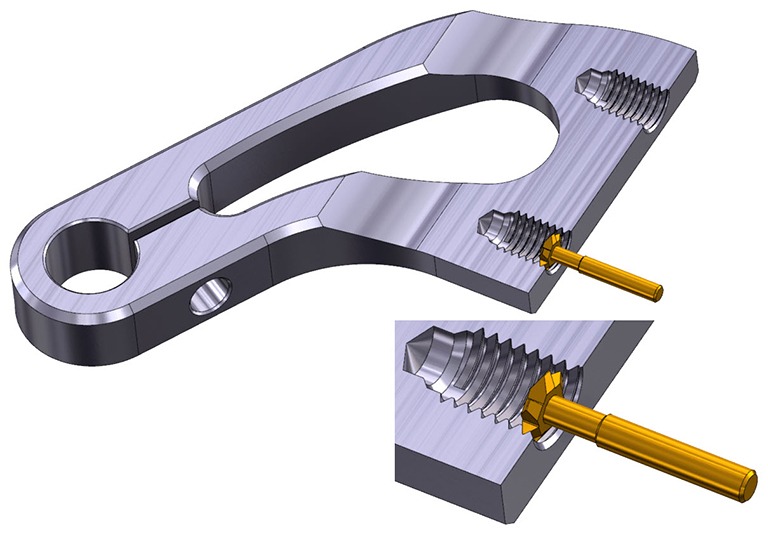
Cutter Compensation Moves: Thread Mill now features the new Plunge after first move and Retract before last move parameters. These parameters define, optionally through the Line lengths fields, a linear move at the feed plane that occurs before and after the cutter engagement. This means you can define the linear motion outside of the machining area for enabling and disabling cutter compensation. The Line length fields specify the length of the linear moves.
Often when using thread mill tools, the tool diameter and the diameter of the hole being machined are close in size. This means it is not possible to move the tool linearly before engaging in the cut, as required by most machines when enabling and disabling cutter compensation. Use the Plunge after first move and Retract before last move parameters to solve this problem.
Directional Cutting: The new Cutting Direction and Spindle Direction fields found on Thread Mill’s parameter page not only increase visibility, but also provide better control over the cutting direction due to the influence of the Tool page’s Spindle direction parameter on the cutting direction.
Lead In/Out Options: New options in the Lead In/Out page add tool manufacturer-recommended helical functionality. The new options also provide control over cutter compensation and overriding entry speeds and feeds.
Line Length Controls: When you enter values in the new Line Lengths controls, Mastercam constructs a line perpendicular to the entry and exit moves. You can also use this feature to enable and disable cutter compensation outside of the diameter to be machined. You would apply this where the hole diameter is too small for the moves to take place within the machining area.
Tool Edge Feed Rate: Use the new Tool Edge feed rate checkbox to calculate the feed rate based on the tool’s tangential edge rather than on the centerline. Tool edge feed rate produces a more accurate feed rate based on the cutter diameter and the diameter of the hole being machined. It also allows you to program Thread Mill operations with a higher level of accuracy, which helps achieve proper tool wear and a more efficient toolpath. Save time by automatically calculating the proper feed rate for Thread Mill, rather than the need to manually calculate the feed rate at the edge of the tool’s diameter.
Want More Information?
If seeing the top Milling features has you ready to update or you want to learn more about what Mastercam can do for your shop, please reach out to your local Mastercam Channel Partner. Or, if you’re ready to explore Milling features on your own, download the free Mastercam Learning Edition.
1. Saving and Loading Machine Configurations
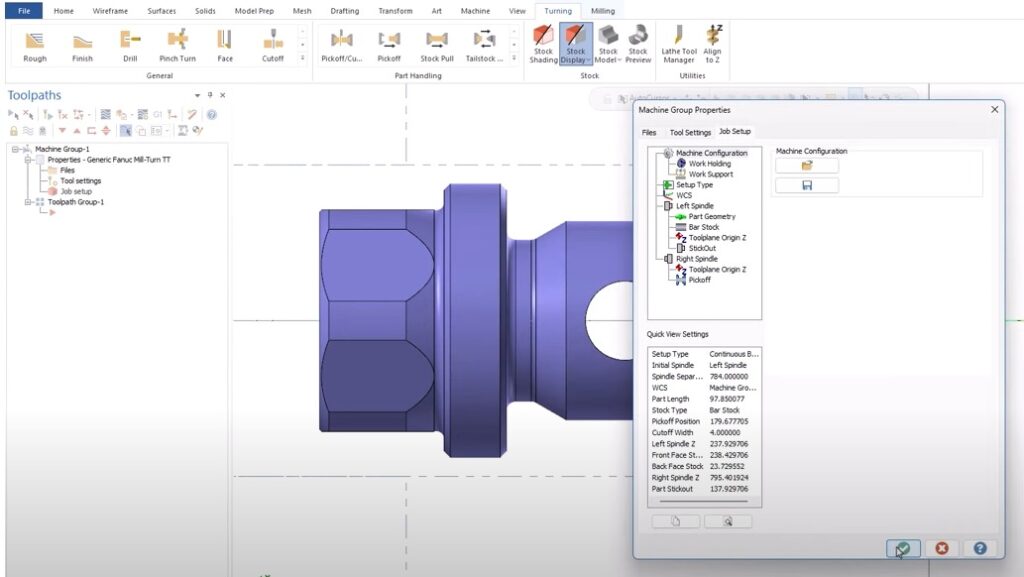
In Mastercam 2025, Mill-Turn users now have the capability to save unique machine configurations into individual files, streamlining setup for new projects. This advancement is super useful when processing families of parts or when you have tools and fixturing that rarely leave the machine.
Your configuration file can be stored anywhere on your workstation! Power users can store the configuration right in the Mill-Turn’s respective .machine file under the “Machine Configuration” files node.
2. Analyze Deviation
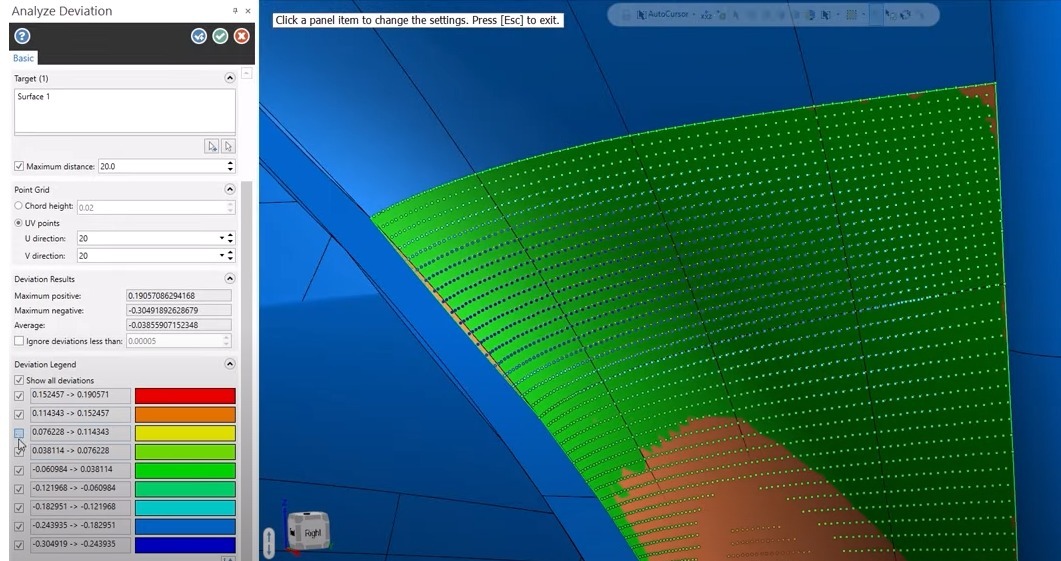
Mastercam 2025 introduces a new suite of tools designed to help analyze your CAD models. The new Analyze Deviation function includes an assortment of tools to help measure distances between multiple entities.
Whether you need to measure distances between surfaces, curves, or points –this function can help identify distances between any combination of these entities and display the results in an easy-to-read graphical interface.
The Analyze Deviation function is extremely versatile and can help you analyze your models, so you know exactly what you’re working with.
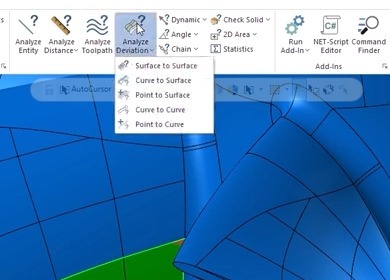
3. Solid Hole Selection
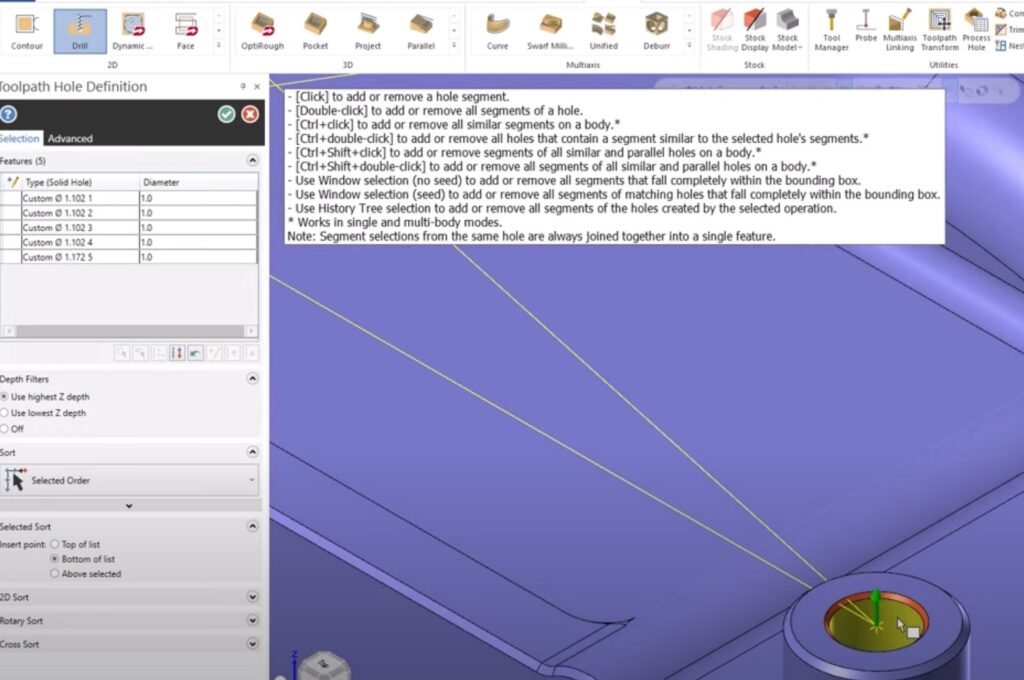
In Mastercam 2025, Solid Hole selection capabilities were expanded to provide users with a much more efficient workflow. You can now save a lot of time by not requiring the use of the Find Hole function before making Solid Hole selections.
Mastercam 2025 can now select hole shapes directly from the solid body without model history. Even parts imported directly from other CAD formats can have the hole features directly selected. We have also added more filters to select multiple hole features more intelligently.
These new Solid Hole selection changes greatly improve Mastercam’s hole making workflow, increasing efficiency and gives users more control over programming hole features.
4. Finishing Passes for Dynamic Toolpath
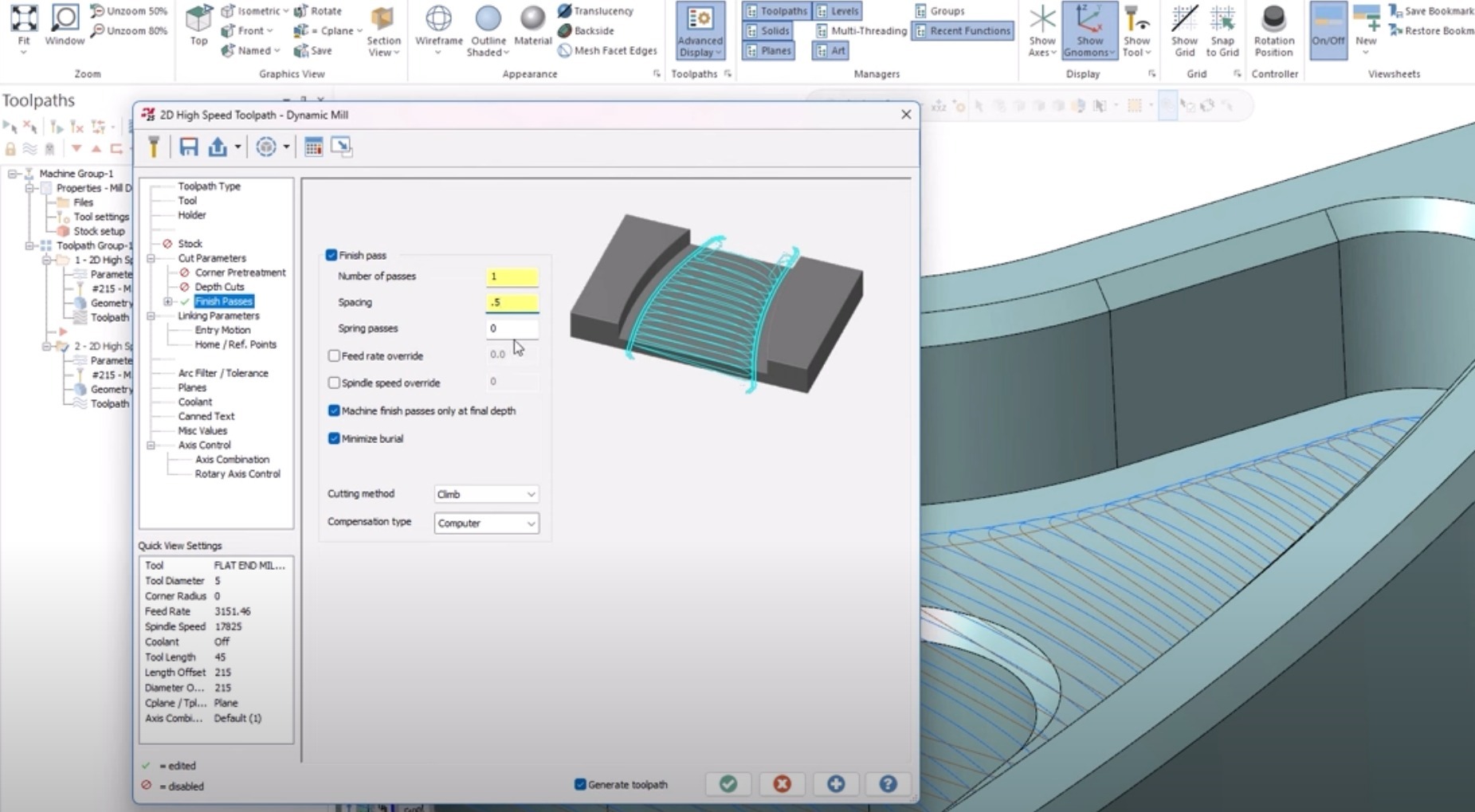
Mastercam’s Dynamic Toolpath functionality has been a game changer in the world of manufacturing. It reduces cycle times, increases tool life, and minimizes wear and tear on your machines.
In Mastercam 2025, we have continued to enhance this toolpath motion with the addition of finish passes. We have also added a Minimize Burial option to keep your tool from over-engaging in both 2D Dynamic Mill and Area Mill toolpaths. This enhancement will streamline your programming process when working with these popular toolpaths.
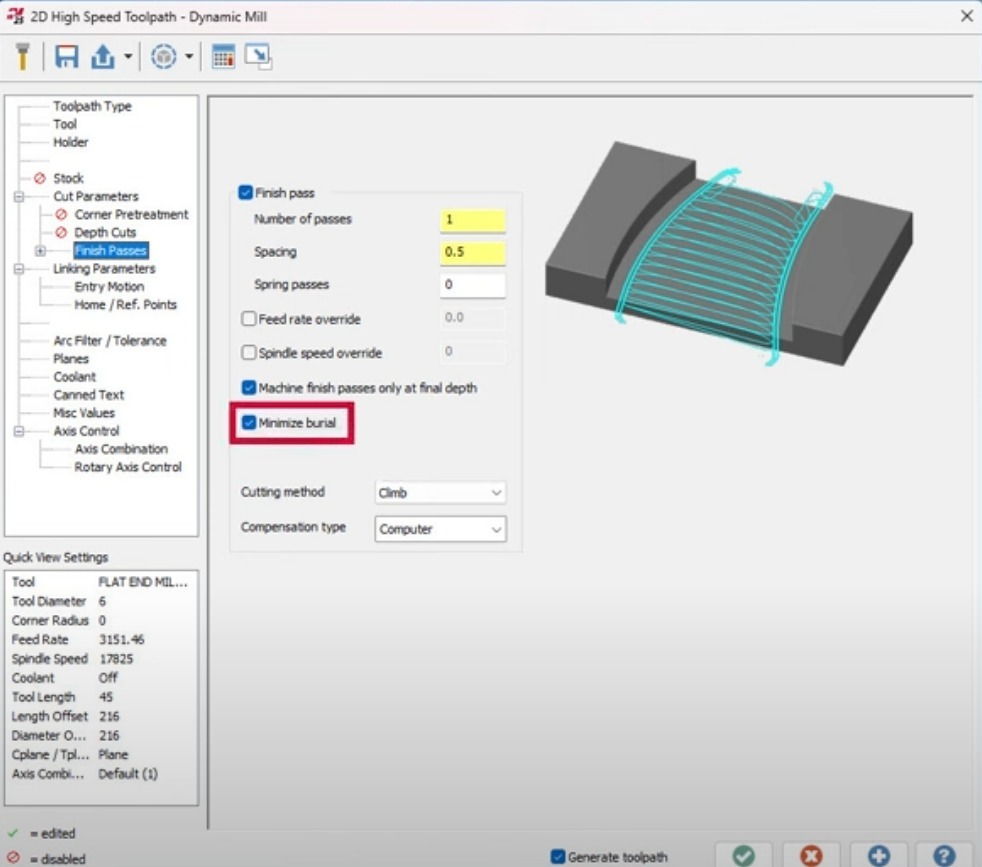
5. Improvements to Multiaxis Safety Zone
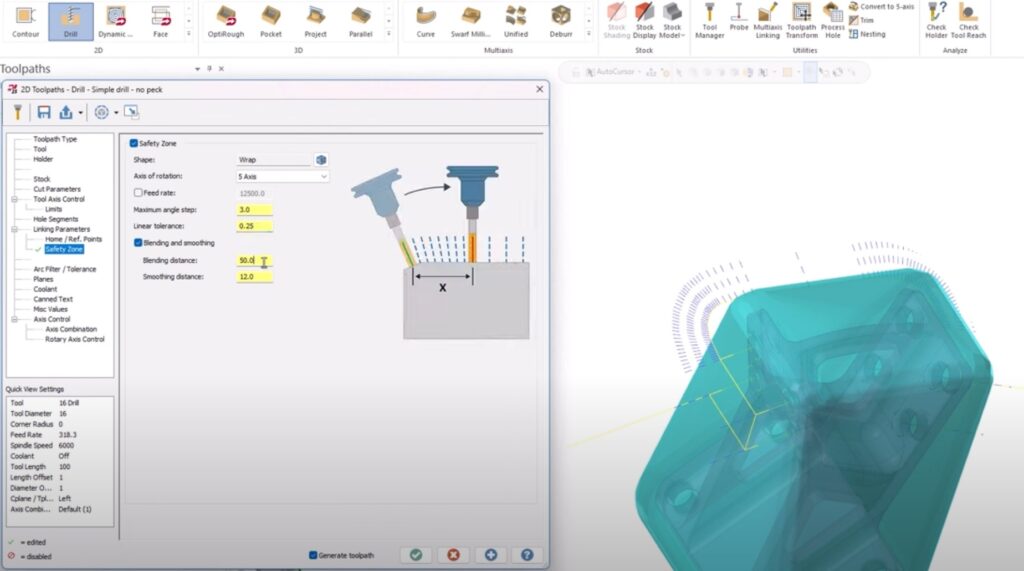
Safety Zone for hole making has been overhauled in Mastercam 2025 with a new algorithm for improved transition movement. This enhancement has allowed us to introduce new parameters, so users have more control over transition motion.
In Mastercam 2025, Safety Zone will now use a mesh in the background for all the defined shapes in the Safety Zone panel for the linking calculation. The ability to edit the vectors with respect to the Safety Zone shape results in better tool-angle motion for linking moves.
These new parameters in the Safety Zone page include a linear tolerance value, blending distance, and smoothing distance values.
Learn More
If you’re serious about streamlining the workflow in your shop, your local Mastercam Channel Partner is one of your most valuable assets to talk to about upgrading to Mastercam 2025. Reach out to yours here!